Phase 2 Mission Task:
Read the Phase 2 Mission Task
In Phase 2 of this Challenge, teams will design, build, and test terrestrial analog full-scale prototypes of robotic icy regolith excavation and transportation systems. The goal of Phase 2 is to demonstrate long term operations and durability of icy regolith excavation and transportation equipment. Downstream ice and/or water delivery equipment described in Phase 1 of this Challenge will not be considered in Phase 2 of this Challenge.
Excavation will be demonstrated by extracting simulated icy regolith from a test bed as described in the Icy Regolith Simulant section (Section 3.2.5 in the Phase 2 Rules document). Transportation will be demonstrated by hauling excavated icy regolith simulant over a surface which simulates certain physical characteristics of the expected lunar surface as described in the Transportation Demonstration Area section (Section 3.2.6 in the Phase 2 Rules document).
Equipment Design Requirements
- All hardware and equipment must be designed at full scale:
- Total system mass must be less than 10,000 kgs
- Total system must notionally fit inside a 6 meter diameter, 10 meter long cylinder
- Total system includes:
- all icy regolith excavation equipment
- all icy regolith transportation equipment (can be the same robot as above)
- any spare parts that might be needed during the long-term durability demonstration test regimen
- any tools and equipment that might be needed for repair and maintenance during the long-term durability demonstration test regimen
- any tools and equipment that might be needed to maintain the test area during the long-term durability demonstration test regimen
- Icy-regolith excavation and transportation equipment:
- Must not use wired umbilical power. Only onboard power sources will be allowed (i.e. batteries, etc.)
- Must not use wired communications. Only wireless communications equipment will be allowed (i.e. WiFi, Bluetooth, RF, etc.)
- Must not employ any fundamental physical processes, gases, fluids or consumables that would not work in a lunar environment. For example:
- pneumatic systems are allowed only if the gas is stored and supplied onboard the robot itself
- hydraulic fluid systems are not allowed unless the power and mass for a fully encapsulating heating system is included that would be capable of keeping the fluid from freezing in the extreme environmental conditions on the lunar surface
- air-filled or foam filled rubber tires are not allowed, as they would not maintain their integrity in the vacuum of the lunar surface
- ultrasonic sensors are not allowed, as they would not function in a vacuum
Electronic and mechanical components are not required to be space qualified for Lunar atmospheric, electromagnetic, nor thermal environments. The Challenge rules are intended to require robots to show an off-world plausible system functionality but the components do not have to be traceable to a space-qualified, radiation-hardened version.
Examples of allowable terrestrial components are: sealed lead-acid batteries, nickel metal hydride batteries, rubber or plastic parts, fan-cooled electronics, and motors with brushes. If a team has a question about the acceptability of a specific terrestrial component, please send the question to admin@breaktheicechallenge.com to receive official guidance.
Since teams will be performing their long-term durability demonstrations of their prototype systems at terrestrial locations under ambient environmental conditions, working thermal protection systems appropriate for an extreme lunar environment (i.e., motor heaters, electronics heaters, radiators, etc.) will not be required. Working onboard lighting systems appropriate for an extreme lunar environment will also not be required.
Durability Demonstration Test Requirements
- Durability demonstration must be performed at a terrestrial location of each team’s
- Demonstration must include both an excavation subsystem and a transportation subsystem. The transportation subsystem must haul only the material that was previously excavated by the excavation subsystem.
- Demonstration must be performed under ambient conditions (temperature, lighting, atmospheric pressure, naturally occurring dust levels, earth gravity, etc.).
- Teams will target operation of all prototype equipment over a period of 15 full, 24-hour long, earth days, or until equipment fails.
- The excavation subsystem must extract simulated regolith defined in Section 3.2.5.
- Teams will target excavating 12,000 kg of simulated regolith.
- Teams must start the demonstration using an undisturbed slab of simulated regolith.
- The transportation subsystem must be performed in an area that complies with the requirements of Section 3.2.6 of the Phase 2 Rules document.
- The transportation component must haul material that was excavated during the excavation component of the demonstration.
- Teams will target transporting and delivering 12,000 kg of simulated regolith.
- Transportation equipment must haul material 500 meters (one way) to a delivery location.
- Transportation equipment must return 500 meters back to the excavation location following delivery of material.
- This 500-meter one-way distance is representative of the distance between the Excavation Site and the NASA Water Extraction Plant detailed in the Mission Scenario.
- Please note per Section 3.2.6 that the 500-meter travel distance requirements can be met inside a small area as long as the equipment’s onboard odometry sensor accurately reads 500 meters per each one-way trip.
- Human intervention with the prototype icy regolith excavation and transportation equipment is allowed during the long-term durability demonstration with the following caveats:
- prototype icy regolith excavation and transportation equipment can be either remotely controlled by human operators or fully autonomous or anywhere in-between
- in case of excessive wear or breakdown, manual repairs and parts replacement are allowed, provided worn parts are saved for inspection and details of excessive wear and breakdowns are included in the final Durability Demonstration Test Report, as detailed in section 3.2.9.2 of the Phase 2 Rules document
- any spare parts that might be needed during the test:
- must have been identified in the Durability Demonstration Test Plan
- must be on hand throughout the Durability Demonstration
- must have been weighed and their mass counted as part of the total mass of equipment
- examples of spare parts include spare tires, swapped out batteries, spare electronics, spare digging teeth, redundant robots, redundant subsystems, etc.
- any tools and equipment that might be needed for repair and maintenance of prototype icy regolith excavation and transportation equipment during the test:
- must have been identified in the Durability Demonstration Test Plan
- must be on hand throughout the Durability Demonstration
- must have been weighed and their mass counted as part of the total mass of equipment
- energy consumed by tools and equipment during prototype icy regolith excavation and transportation equipment repair and maintenance will not be collected nor reported as part of the total energy used by the system
- examples of tools and equipment for repair and maintenance include jacks, cranes, toolboxes, power tools, hand tools, etc. (humans using the tools and equipment do not need to be weighed and counted)
- the 15-day timer must not pause for any prototype equipment repair and maintenance activities
- if equipment fails prior to the end of the 15-day durability demonstration test and no spare parts are available for repair, the durability demonstration must be terminated early
Icy Regolith Simulant
The simulated icy regolith utilized by teams for long duration excavation demonstration shall meet the minimum requirements provided below. Teams shall submit mixture design, certified test report, and a geometry sketch of their icy regolith simulant for review per deliverables and schedule in Phase 2 Rules.
Concrete materials will be used to simulate the assumed mechanical properties of 4% water weight lunar icy regolith. The 10% water weight icy regolith detailed in the Phase 1 Rules of this Challenge will not be simulated nor utilized in Phase 2.
- Simulated icy regolith shall be made from Controlled Low Strength Materials (CLSM) following the guidance provided in the American Concrete Institute report, ACI 229R Report on Controlled Low-Strength Materials (available at https://www.concrete.org).
- There are no specific requirements or testing of bulk density or tensile strength.
- Lightweight aggregates are not permitted.
- Simulated icy regolith shall be proven to have an unconfined compressive strength of 1.5 to 2.0 MPa at the start of the Durability Demonstration Test.
- ASTM C39 Compression Test of 150 mm by 300 mm cylinders are recommended for verifying compressive strength.
- The geometry of the icy regolith simulant is as follows:
- The depth of the simulated material to be excavated shall be no more than 80 cm.
- The width and length shall be any dimensions necessary to accommodate the equipment under test. Any shape (square, rectangular, circular, etc.) is also acceptable.
- A minimum of 20 cm of additional buffer area (an area not to be excavated) shall surround the volume to be excavated in order to minimize the likelihood of a crack that propagates through the boundary of the deposit. See Figure 2.
- Simulated material to be excavated shall be placed in one continuous pour.
- Dry (0% water) over burden shall not be simulated.
Figure 2. Side view of icy-regolith simulant bed, buffer area shown in green
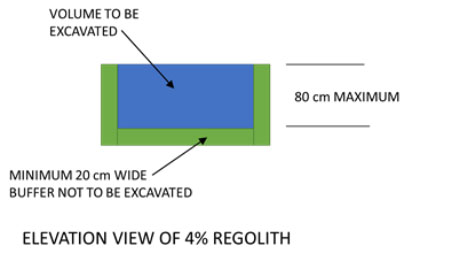
Transportation Demonstration Area
Rather than prescribing a specific track size, shape, length, roughness, layout, slope, track surface makeup, particle shape, mineralogy, size distribution, compaction, etc, this Challenge allows each team to create their own transportation demonstration area capable of demonstrating and testing terrestrial analog full-scale prototypes of robotic icy regolith transportation systems continuously for 15 days. Teams must explain and justify the extent to which their transportation demonstration area simulates the physical and environmental details of the anticipated lunar surface.
The area used for long duration transportation demonstration shall meet the minimum requirements provided below. Teams shall submit plans and specifications for their transportation demonstration area for review per deliverables and schedule in Phase 2 Rules.
- The minimum one-way travel distance shall be 500 meters from simulated Excavation Site to simulated Water Extraction Plant.
- This 500 meter travel distance can be performed inside a small area by following multiple paths that are less than the one-way distance, as long as the equipment’s onboard odometry sensor accurately reads 500 meters per each one way trip.
- Transportation equipment shall drive in the transportation demonstration area in both directions equally. In other words, equipment will drive in one direction to get to the simulated Water Extraction Plant and then drive in the opposite direction to return to the simulated Excavation Site
- The surface of the transportation demonstration area should simulate the surface conditions expected by the team’s delivery architecture.
- The prototype robotic icy regolith transportation system must repeatedly drive on the same path throughout the Durability Demonstration Test.
- Teams must simulate the regolith delivery to the Water Extraction Plant (detailed in Phase 1: Mission Scenario section) to the following fidelity:
- The designated delivery location for the simulated regolith must be capable of receiving and weighing the material that was hauled and delivered by the prototype robotic icy regolith transportation system.
- Once delivered, material must be weighed either automatically or manually within the designated delivery location.
- Once weighed, material may be removed either automatically or manually from the designated delivery location.
- Teams must target a delivery rate of 800 kg every 24 hours.
- A daily delivery that is within plus or minus 10% of the target rate is acceptable. Deliveries greater than or less than the target range will have a negative effect on scoring.
- The designated delivery location for the simulated regolith must be capable of receiving and weighing the material that was hauled and delivered by the prototype robotic icy regolith transportation system.
- Human intervention with the transportation demonstration area is allowed during the long-term durability demonstration with the following caveats:
- robotic maintenance equipment can be either remotely controlled by human operators or fully autonomous or anywhere in-between
- only robotic maintenance of the transportation demonstration area is allowed – human held tools and equipment are not to be used to maintain or repair the transportation demonstration area once the Durability Demonstration Test has started
- robotic maintenance equipment that might be needed for transportation demonstration area repair and maintenance during the test:
- must have been identified in the Durability Demonstration Test Plan
- must be on hand throughout the Durability Demonstration
- must have been weighed and their mass counted as part of the total mass of equipment
- energy consumed during transportation demonstration area repair and maintenance will not be collected nor reported as part of the total energy used by the system
- examples of robotic maintenance equipment for repair and maintenance of transportation demonstration area include earth moving equipment, surface preparation equipment, soil compaction equipment, rock moving equipment, etc.
- the 15 day timer must not pause for any transportation demonstration area repair and maintenance activities
- if robotic maintenance equipment fails prior to the end of the 15 day durability demonstration test and the transportation demonstration area conditions can no longer be sufficiently justified as simulating the physical and environmental details of the anticipated lunar surface, the durability demonstration must be terminated early
- robotic maintenance equipment can be either remotely controlled by human operators or fully autonomous or anywhere in-between
Data Collection
During the long-term durability demonstration, the following data must be collected by the team:
- At least one live 1080 line or better resolution video stream that is either publicly accessible or is privately accessible to the Centennial Challenges Judging Panel
- This live feed must be broadcast during the entire 15-day duration of the durability demonstration test
- Separate video feeds focusing on each major piece of hardware and equipment being demonstrated (excavator, regolith transporter, etc.) are required
- Detailed photos of each major piece of hardware and equipment performing normal operations
- Mass of each piece of equipment, including spare parts and repair and maintenance tools on standby whether used or unused during the demonstration, plus total system mass
- Energy used by each piece of prototype icy regolith excavation and transportation equipment, plus total system energy
- Energy usage must be collected using commercial-off-the-shelf energy data logger devices.
- Each energy data logger device must be installed in series (inline) with the robot’s energy source (battery pack) in order to track total energy used by the robotic system.
- Energy consumed by tools and equipment during prototype icy regolith excavation and transportation equipment repair and maintenance will not be collected nor reported
- Energy consumed by tools and equipment during transportation demonstration area repair and maintenance will not be collected nor reported
- Runtime of each piece of equipment, plus total system runtime, plus total number of icy regolith excavation and transportation robots
- Runtime can be collected using commercial-off-the-shelf sensors, or it can be logged manually by test staff
- Runtime is defined as any motion of the equipment under test (for example, digging, driving, dumping, etc). Down time, idle time, recharge time, etc. is not considered runtime.
- Total distance traversed by icy-regolith transportation equipment during transportation of material from the excavation location to the delivery location, plus total number of icy-regolith transportation equipment round trips between simulated Excavation Site and simulated Water Extraction Plant
- Distance traversed can be collected using commercial-off-the-shelf sensors, or it can be logged manually by test staff
- Number of round trips can be collected automatically by proximity or other applicable sensors, or it can be logged manually by test staff
- Compressive strength of icy regolith simulant at the beginning and end of the 15 day test period.
- Total amount (kg) of icy regolith simulant excavated and delivered
- A daily record (at the end of each 24 hour period) of the mass of regolith delivered.
- Any material processed by the excavation equipment which is not also transported and delivered by the transportation equipment will not be scored and should not be reported.
- Log of parts replaced, breakdowns, issues requiring human intervention, along with job-hours spent on repairs and maintenance on the prototype icy regolith excavation and transportation equipment.
- Log of any maintenance or repair to the Transportation Demonstration Area.
Onsite Observation Visits
The Break the Ice Challenge judging staff will visit all the Teams that are eligible to win prizes during the course of long-term durability demonstrations. Notice of an on-site observation visit will be provided to the team lead at least 24 hours prior to arrival of the judging staff. Each site visit is expected to be completed within the span of two days. Teams must satisfy the following requirements relating to onsite visits:
- Notify the Break the Ice Lunar Challenge organizers of anticipated start date of durability demonstration a minimum of 28 days in advance of anticipated start date. Any changes to the start date of the test after sending this notification must be immediately communicated with a justification for the change. All notifications must be sent to admin@breaktheicechallenge.com.
- Upon arrival, provide the Break the Ice Lunar Challenge judging staff judging staff with the following:
- Appropriate personal protective equipment
- Detailed tour of testing site, including excavation component, transportation component, icy-regolith simulant
- Detailed tour of the hardware and equipment under test
- Detailed tour of planned spare parts and repair tools